
Type 200
Fixed Drive Rollers
Sprocket Welded Rollers

Features
-
Drive - Fixed Drive with Sprocket
-
Materials - Carbon Steel / Stainless Steel
-
Bearing Housing - Polymide Molded
-
Sizes - Roller Dia. & Shaft combination as per standard table below
-
Length - made to order
-
Load Capacity - reference table below
-
Surface Treatments
-
Carbon steel - Zinc Plated, Chrome plated
-
SS - Mirror Polished
-
-
Coatings - PU Coated, PVC Sleeve
Standard Sizes available in
Type200 Sprocket Driven Rollers
This roller construction is similar to Interroll make Series 3500 Fixed Drive Conveyor Roller
The Comibation of Roller Dia x thick x Shaft Dia is Fixed and Lengths are variable as per customer requried.
Load Capacity of Conveyor Rollers
Understanding Load Capacity: Navigating Roller Dynamics
Explore the dynamics of load capacity with Excel Conveyors. Our table showcases load capacities, but it's important to note that these figures are reference points. The actual load-bearing capabilities depend on factors such as material composition and working conditions.
Designers and users of roller conveyors must grasp a crucial concept: the load-carrying capacity of rollers is distributive, not concentric. In simpler terms, it's not a pinpoint load capacity. The capacity is distributed along the length of the roller.
As a key insight, load-carrying capacity operates inversely to roller length. Longer rollers experience a decrease in capacity. This relationship is pivotal for designers and users to comprehend. For applications involving high-width products, the solution lies in opting for larger diameters to ensure optimal load support.
At Excel Conveyors, we empower you with knowledge to make informed decisions. Remember, our load capacities are indicative, and real-world conditions play a significant role. Dive deeper into the intricacies of load dynamics to enhance the efficiency and reliability of your conveyor systems. Your success is our priority.
Please note that the Load capacity is mentioned in Kgs in below Table
Visit our calculator page to use ready calculator
Sprocket Driven Rollers Coating Options
Conveyor Rollers have lot of coating options available as below.
Zinc Plating
-
Also known as Zinc Blue white passivation
-
This is most widely done coating process for Rollers
-
It gives 3-5 micron shiny white appearance
-
Cost effective process
-
Fast compared to other process.
-
This process is used in packaging areas where carton boxes, crates etc are to be conveyed
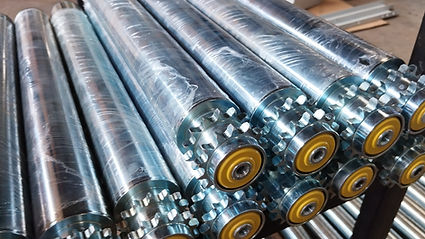
Chrome Plating
-
This process is done vary rarely
-
When there are chances of scratches on the roller, then this process is done to protect the roller.
-
It gives 5 micron shiny white appearance
-
The coating thickness can be increased
-
Very Costly process
-
Very Time Consuming, compared to other process.
-
Auto-ancillary companies prefer this process when conveying metal parts
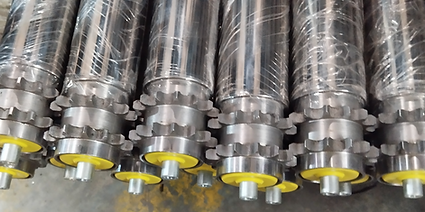
PU Coated Rollers
-
PU is polyurethane Coating
-
This process is done when the conveying parts is metal and it needs to be protected from scratches or metal to metal friction.
-
Generally a 4-5 mm thickness layer is done on the roller.
-
The coating thickness can be increased
-
Very Costly process & Very Time Consuming, compared to other process.
-
Auto-ancillary companies prefer this process when conveying metal parts
-
Roller Dia. 31.75 is PU Coated to 40mm OD
-
Roller Dia. 38mm is PU coated to 48 or 50mm OD
-
Roller Dia 51 mm is coated to 60mm OD
-
Roller Dia 60.3mm is coated to 70mm OD
-
It is available is various colors as Green, Yellow, Red etc
-
It gives smooth bright and shiny finish
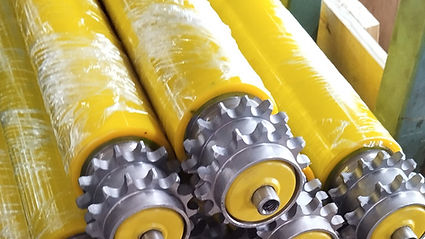
PVC Sleeve Coated Rollers
-
The PVC sleeve is 2-2.5mm thick.
-
It is inserted on the roller with high pressure.
-
It is used when you want friction or grip on the rollers
-
Tedious process

Choosing Sprocket Driven Rollers for Optimal Conveyance
Sprocket Driven Conveyor Rollers emerge as the preferred choice when precision in object movement is paramount, especially in scenarios involving motorized roller conveyors.
Here's why and when you should opt for this dynamic solution:
-
Motorized Efficiency: Sprocket Driven Rollers shine in motorized roller conveyor systems, ensuring a seamless transfer of objects, be it carton boxes or other materials.
-
Machined Precision: Our rollers boast fully machined sprockets welded to the roller pipe and meticulously assembled with a shaft. This ensures a robust and precise connection, minimizing the risk of slippage between the chain and sprocket.
-
Versatile Load Handling: Chain and sprocket combinations are a versatile option suitable for both light and heavy-duty applications. The availability of various size options caters to diverse load requirements.
-
Proven Reliability: The time-tested reliability of the chain and sprocket combination makes it a preferred choice. Its dependable nature ensures efficient operation without slippage, providing a robust solution for material handling.
-
Easy Maintenance:Chain driven live roller conveyors simplify maintenance and replacement procedures. The straightforward design facilitates easy handling, making it user-friendly and accessible even for those without extensive technical expertise.
-
Gap Opportunities: The inherent gaps between rollers offer additional applications, such as the installation of stoppers or specific washing systems. This flexibility enhances the practicality and adaptability of the conveyor system.
-
Long-Standing Tradition: The use of chain and sprocket combinations has stood the test of time, proving its reliability across generations. The familiarity with this system makes it easily understandable and manageable for operators.
In summary, Sprocket Driven Rollers with chain and sprocket mechanisms are a go-to solution for those seeking efficiency, reliability, and adaptability in material handling. Whether for light or heavy-duty applications, these rollers offer a time-honored and trusted solution for seamless conveyance in various industries.